I have 8 new hubs and 8 new axles that I had made at a shop near my home.
The holes in the hubs are the same ID as the axles OD, but of course when I slide them together I get a little play. If I weld without somehow centering them, I am certainly going to have some wheel wobble going on.
Here's a pic of them both on my work bench, I have a square zip tied to the axle to illustrate my point.
Is there a tool of some sort to keep the axle centered as I start to weld?
The holes in the hubs are the same ID as the axles OD, but of course when I slide them together I get a little play. If I weld without somehow centering them, I am certainly going to have some wheel wobble going on.
Here's a pic of them both on my work bench, I have a square zip tied to the axle to illustrate my point.
Is there a tool of some sort to keep the axle centered as I start to weld?
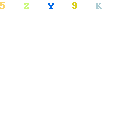
Comment