I've just about put the finishing touches on the poly skid plate on the Chief. The bottom was cracked in a few spots, and quite frankly, I feel there is no "ultimate fix" to a cracked bottom of you want it to be waterproof, and want to be able to actually use an AATV for its intended purpose. Other fixes include riveting steel to the body(heavy), using fiberglass resin and mat (OK, but doesn't stand up to abuse well) and other methods, but I wanted something that would really take what I wanted to dish out on the machine.
The skid plate is a full 1/4" thick HDPE that is in two pieces. I would have used one sheet, but it had to be cut for shipping. It turns out that two pieces was a bit easier. Its held on with 72 (or so) steel shank waterproof rivets that RI uses on their machines. I was dismayed that I couldn't get the poly to wrap up around the sides well enough to incorporate into the axle flanges. It's plenty strong, though. I'm just not entirely pleased with how it terminates so abruptly on the bottom.
The forming was done with a heat gun. It works tremendously well, as long as you're patient. There was a lot of force with jacks to bend the poly and hold it in place once it was good and mushy. It incorporates the rear trailer hitch, and it has two threaded drain plugs I've added since the pictures were taken. The first time I had it out (and many times since then) I've been forging through the brush and found that I suddenly stopped forward progress altogether. Each time, I was centered on a different large boulder. No cracking, thumping, creaking or anything. It just rides up it and stops. There's virtually no deformation in the body, either. I can jack up the entire machine with a floor jack right in the center of the body. It was quite a bit of work, but well worth it to keep the 'ol gal around for a few more years. There's no water around here yet, so I haven't had the opportunity to check for water-tightness.
I recommend it to anyone with a body that they're thinking about junking because of lower tub issues. The pics aren't great, but you get the idea. More pics in my gallery...
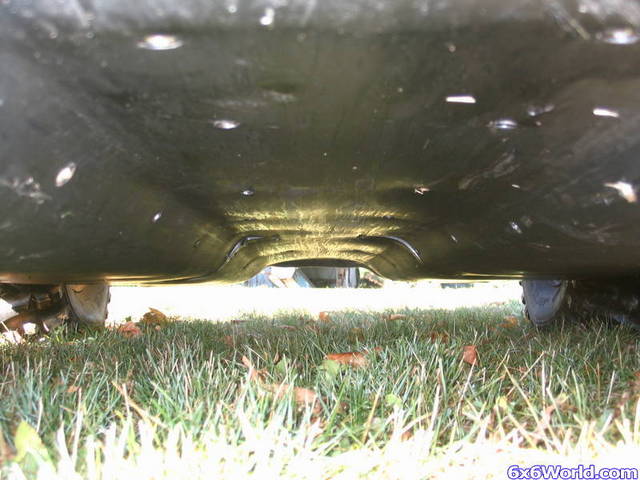
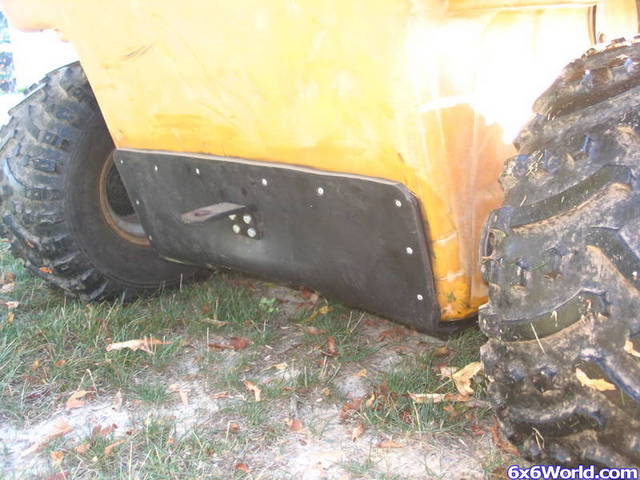
The skid plate is a full 1/4" thick HDPE that is in two pieces. I would have used one sheet, but it had to be cut for shipping. It turns out that two pieces was a bit easier. Its held on with 72 (or so) steel shank waterproof rivets that RI uses on their machines. I was dismayed that I couldn't get the poly to wrap up around the sides well enough to incorporate into the axle flanges. It's plenty strong, though. I'm just not entirely pleased with how it terminates so abruptly on the bottom.
The forming was done with a heat gun. It works tremendously well, as long as you're patient. There was a lot of force with jacks to bend the poly and hold it in place once it was good and mushy. It incorporates the rear trailer hitch, and it has two threaded drain plugs I've added since the pictures were taken. The first time I had it out (and many times since then) I've been forging through the brush and found that I suddenly stopped forward progress altogether. Each time, I was centered on a different large boulder. No cracking, thumping, creaking or anything. It just rides up it and stops. There's virtually no deformation in the body, either. I can jack up the entire machine with a floor jack right in the center of the body. It was quite a bit of work, but well worth it to keep the 'ol gal around for a few more years. There's no water around here yet, so I haven't had the opportunity to check for water-tightness.
I recommend it to anyone with a body that they're thinking about junking because of lower tub issues. The pics aren't great, but you get the idea. More pics in my gallery...
Comment